How Much Does a Building Management System Cost and Why It’s Worth It
April 2nd, 2025
4 min read
By Dennis Allen
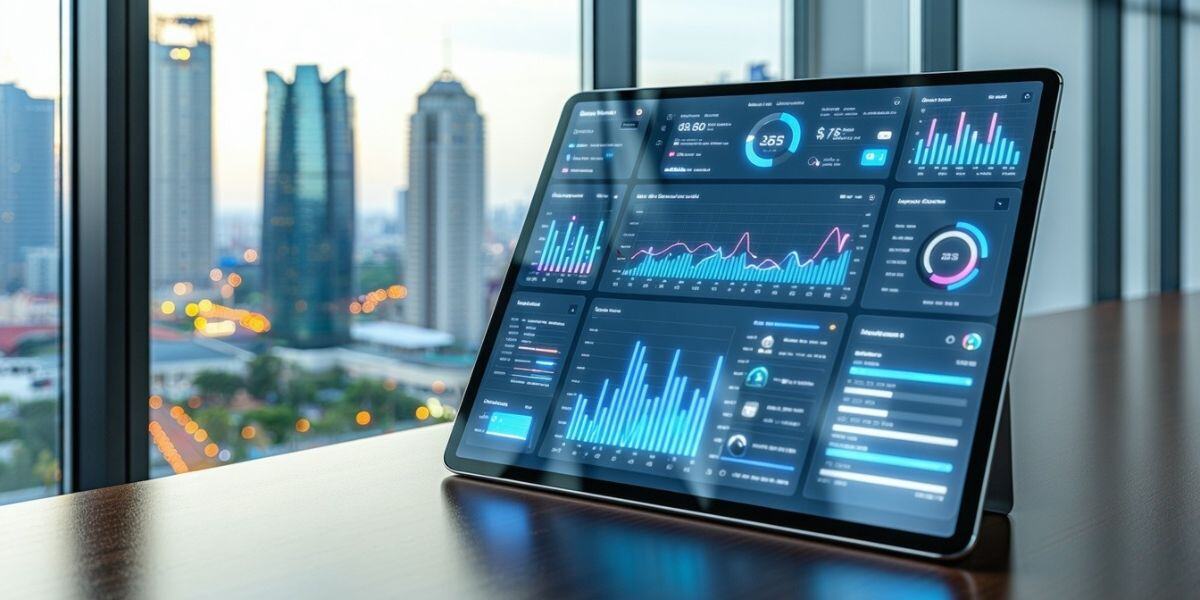
If you own or manage a commercial building, you know how complex it can be to keep everything running smoothly. HVAC, lighting, security, and energy consumption all require constant monitoring. Without a Building Management System, these tasks can become time-consuming and expensive. Energy waste, unexpected repairs, and inefficiencies add up quickly, affecting your bottom line.
At Harold Brothers, we specialize in the commercial plumbing and heating aspects of building automation. We’ve worked with businesses across industries to help implement BMS solutions that reduce costs, improve comfort, and enhance overall building performance. With over 16 years of experience, we’ve seen firsthand how investing in a BMS pays off in the long run.
In this article, we’ll explain the cost of a Building Management System and why it’s a smart investment. We’ll cover average pricing, factors that affect costs, and hidden expenses to consider. By the end, you’ll understand how a BMS can save you money while improving your building operations.
What Is a Building Management System and How Does It Work?
A Building Management System, or BMS, is a computer-based system that helps control things like heating, air conditioning, lighting, and security in a building. It helps everything run smoothly and uses less energy.
This makes buildings more comfortable, safer, and cheaper to operate. You can think of it like a smart thermostat for your entire building—it learns what you need, adjusts automatically, and helps save money.
A BMS is like the brain of your building. It thinks for the building, tells each part what to do, and keeps everything working without you needing to check every little thing.
How Much Does a Building Management System Cost for a Commercial Building?
The cost of a Building Management System varies based on the size of the building, the number of integrated systems, and the level of automation required.
You will probably be looking at costs around:
- Small commercial buildings: $50,000 - $300,000
- Mid-sized commercial buildings: $200,000 - $700,000
- Large commercial buildings: $500,000 - $1,000,000+
This pricing includes hardware, software, and installation, but can vary depending on customization needs.
5 Key Factors That Drive Up the Cost of a Building Management System
Several factors affect the final price of a BMS installation, and understanding them upfront can help you better plan your project and avoid surprises down the road.
Knowing these cost drivers also allows you to ask the right questions and choose the system that fits your building's needs and budget.
1. Building Size and Complexity
A larger facility with multiple systems (HVAC, lighting, security, etc.) requires more sensors, controllers, and software capabilities, increasing the cost. Older buildings may require retrofitting, increasing costs.
2. Integration with Existing Systems
If your building has outdated equipment, it may need upgrades or retrofits to integrate with a modern BMS.
3. Advanced Features and Customization
More sophisticated automation features—such as AI-driven energy optimization or remote monitoring via mobile apps—add to the total cost.
4. Professional Installation and Support
Installing a BMS isn’t a DIY project. A professional setup ensures proper functionality and often includes training for your staff on how to use the system effectively.
5. System Scalability and Future Expansion
If you anticipate building expansions or adding new zones later, you may need to invest in a scalable system upfront, which can slightly raise the initial cost. Planning for future upgrades avoids costly redesigns down the road.
How to Reduce the Cost of Installing a Building Management System
Although a BMS is a significant investment, there are ways to manage costs and maximize savings. One approach is to choose a scalable system. Instead of installing a full BMS all at once, you can start with essential systems, like HVAC control, and add features over time. This allows for flexibility while keeping upfront costs manageable.
Another way to save is by taking advantage of local utility incentives. Many energy providers offer rebates and tax incentives for buildings that install energy-efficient systems. These programs can help offset a significant portion of the initial investment.
Lastly, consider cloud-based BMS platforms. Unlike traditional systems that require expensive on-site servers, cloud-based solutions reduce hardware costs and offer easier access to monitoring and controls from anywhere.
Hidden Costs to Watch Out For When Installing Your Building Management System
While most costs are upfront, it’s important to plan for some hidden fees that can affect your budget. Some BMS providers charge annual software licensing fees for access to updates and remote monitoring features. This ongoing cost ensures your system stays up to date and secure.
You should also factor in maintenance and support costs. Although regular maintenance keeps your BMS running efficiently, not all providers include this in the initial price. Some charge separately for support plans and technician visits.
If your building expands or you decide to add new automation features later, expansion costs may arise. These can include additional hardware, configuration time, and integration work.
Lastly, don’t forget about training costs. Your team may need hands-on training to use the system effectively, especially if it includes advanced or customized features. This training helps ensure you get the full value out of your BMS.
Is a Building Management System Worth It?
A Building Management System isn’t just an expense—it’s a strategic investment that provides long-term benefits:
Lower Energy Costs
A BMS reduces energy waste, optimizing heating, cooling, and lighting. Many businesses see a 15–30% decrease in utility bills within the first year.
Improved Building Efficiency
A BMS automates maintenance alerts, preventing costly breakdowns and extending the life of HVAC, plumbing, and electrical systems. It can notify your team when a boiler is short-cycling or a pump is running too long, helping you fix small issues before they become big problems. Pairing your BMS with a solid HVAC maintenance plan can extend equipment life even further
Increased Property Value
A modern BMS enhances property appeal, attracting tenants and buyers looking for energy-efficient buildings.
Enhanced Security and Comfort
With real-time monitoring and remote access, a BMS improves building security and comfort, keeping occupants safe while maintaining an optimal work environment.
Attracting Quality Tenants
Buildings equipped with a BMS often appeal more to potential tenants who value comfort, efficiency, and technology. In a competitive market, having a BMS can make your building stand out and command higher lease rates.
Supporting a Greener, More Sustainable Building
Using a BMS helps reduce energy consumption and your building's carbon footprint. This contributes to sustainability goals, improves your environmental impact, and can help meet LEED or other green building certifications.
Should You Install a BMS in Your Commercial Building?
Managing a commercial building without a Building Management System leads to higher energy costs, inefficient operations, and unexpected maintenance expenses. A BMS helps optimize building performance while saving you money.
Now that you understand the costs and benefits of a BMS, it’s time to consider implementing one in your facility. Whether you start with basic automation or a full-scale system, the investment will pay off through energy savings, improved comfort, and better operational control.
At Harold Brothers, we have installed many HVAC and plumbing systems that integrate with your current or future building management system. Let our team help you evaluate the right solution for your building and ensure a smooth installation process.
Contact us today for a consultation and see how a BMS can transform your building’s efficiency.
Dennis Allen is the Chief Operating Officer and the Director of HVAC for Harold Brothers Mechanical. His current role includes overseeing daily operations in all aspects of the HVAC department from Estimating, Project Management, Equipment and Subcontractor procurement through completion of all HVAC projects. Dennis currently lives in Marshfield, Ma with his Wife of 15 years and their 2 children. Dennis is very involved in town youth sports and volunteers with Marshfield Youth Soccer and Hockey. You will see him at hockey rinks and soccer fields throughout New England on most weekends, when Dennis is not at the rink or fields, he enjoys spending time with family and friends and is frequently spotted fishing in Duxbury Harbor. Dennis takes pride in his upbringing in the mechanical industry, he started as an apprentice in 2001 and has worked his way up through hard work and dedication in his field. He has worked on multiple large-scale projects throughout his career and credits his development to the tradesman who took him under their wing and provided the knowledge needed to succeed. In his current role he works closely with property owners and engineers to assure each and every project is designed to meet each client’s needs. He is very passionate in the success of the younger generation getting into the field and has donated his time to teach and educate field personnel on how to interpret design documents, installation practices and understanding of current codes. He believes all people regardless of background should be given the opportunity to enter the Pipefitting/Refrigeration industry and be set up for success. He recognizes that his industry is facing a major skilled trade shortage and is firm in his belief that training and education should be made available to all people looking to enter the trade. In 2016 he had the foresight to see our industry was evolving to more energy efficient systems and took a trip to Japan to educate himself on the Variable Refrigerant Flow systems which we currently see being implemented in designs throughout the commonwealth. The people of Japan have been utilizing this technology since the 1970’s and provided invaluable insight into how these systems get manufactured, installed and operate. In 2024 Dennis was appointed a member of the Massachusetts Board of Pipefitters, Refrigeration Technicians, and Sprinkler Fitters.