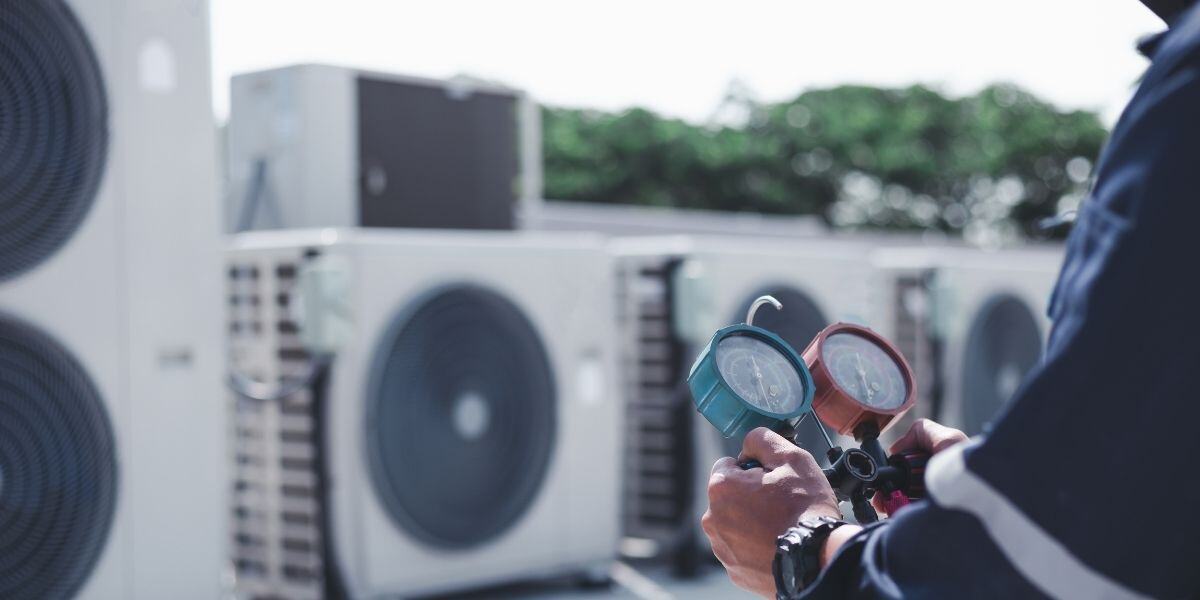
If you own a business in New Hampshire, you know how important it is to keep your heating and cooling system working well. The winters are freezing, and the summers can be hot and humid. Your HVAC system has to work extra hard to keep your building comfortable. If you don’t take care of it, it can break down, waste energy, or even get you in trouble with state rules. Fixing problems at the last minute can be very expensive, so regular maintenance is the best way to save money and keep your system running smoothly.
At Harold Brothers, we have spent over 16 years helping businesses understand HVAC costs and maintenance. We know what makes HVAC upkeep expensive, like labor costs, weather changes, and state rules. Our goal is to help businesses make smart choices to save money and keep their systems in great shape.
In this article, we’ll explain the real costs of HVAC maintenance in New Hampshire, including regular check-ups, emergency repairs, and how the weather affects your system. By the end, you’ll know how much to budget and how to keep your costs under control.
How Much Does Commercial HVAC Maintenance Cost in New Hampshire?
On average, HVAC maintenance for a business in New Hampshire costs between $1,000 and $5,000 per year for a mid-sized office building. The cost depends on the type of system you have as well as the size and the layout of your space. Larger buildings with complex systems may pay $5,000 or more each year.
- Routine service visits: $715–$1,500 per visit
- Hourly maintenance rates: $150–$200 per hour
- Emergency repair rates: $275–$300 per hour
- Major component replacements: Several thousand dollars
What Makes HVAC Costs Go Up?
Many factors can cause your HVAC expenses to rise, from emergency breakdowns to labor costs and extreme weather conditions.
Emergency Repairs
If your HVAC system suddenly stops working, emergency repair rates jump to $275–$300 per hour, plus more for nights or weekends. Breakdowns often happen when the weather is extreme, making it uncomfortable for workers and customers. If heating or cooling is essential for your business, you may even have to close temporarily.
New Parts & Replacements
Major parts like compressors and heat exchangers can cost thousands of dollars to replace. Some older HVAC systems need special parts that are hard to find, which can increase costs and take longer to fix.
Labor Costs
In New Hampshire, skilled HVAC technicians earn $35–$80 per hour, which makes repairs more expensive. Since skilled HVAC workers are in high demand, businesses may also have to wait longer for service or pay extra for urgent repairs.
Weather Conditions
Cold winters and humid summers put extra stress on your HVAC system, leading to more maintenance and repairs. Ice, snow, and moisture can clog filters, freeze coils, and wear down important parts faster.
State Regulations & Compliance
Businesses must hire licensed HVAC professionals, which adds to costs but ensures high-quality service. If your system does not meet state rules, you could face fines, lose your warranty, or even be forced to shut down until the issue is fixed.
How to Lower HVAC Repair Costs
There are several strategies businesses can use to lower HVAC expenses, from regular maintenance to upgrading equipment for better efficiency.
Preventive Maintenance Plans
Signing up for a maintenance contract is cheaper than paying for individual repair visits throughout the year. Regular check-ups can catch small problems before they turn into expensive repairs, keeping your system running efficiently. Think of this like an insurance policy vs. paying out of pocket for major surgery.
Scheduling Maintenance in Off-Seasons
Booking maintenance in the spring or fall can lower costs because demand is lower. HVAC technicians are more available during these times, making it easier to schedule service when it’s convenient for your business.
Upgrading to an Energy-Efficient System
Newer HVAC systems use less energy, which can cut utility bills by up to 20%. Some businesses can also get rebates through programs like NHSaves, making the upgrade more affordable.
Regular Filter Changes & Minor Upkeep
Simple tasks like changing air filters can prevent bigger, more expensive problems later. Skipping maintenance is like ignoring a small leak in your roof—it may not seem like a big deal at first, but over time, it can cause major damage and costly repairs.
Is Your Commercial HVAC Equipment Under Warranty?
It depends on your system. New HVAC units often come with warranties that cover parts for 1–10 years, but labor costs may not be included. Even with a warranty, you still need regular maintenance, which is not covered.
- Manufacturer Warranties – Manufacturer warranties cover parts, but you may have to pay for labor. Always read your warranty to know what is covered.
- Warranty Requirements – Many warranties require regular maintenance by a licensed technician. If you don’t follow these rules, your warranty could be voided, and you will have to pay for repairs yourself.Warranty Options
- Extended Warranty Options – Some manufacturers offer extended warranties for an extra cost. These can help protect you from major repair bills in the future.
Unexpected HVAC Costs
Even if a company gives you a price estimate, extra charges can sometimes surprise business owners. These hidden fees can add up fast, making repairs more expensive than expected.
Watch out for:
- After-hours or weekend fees – Emergency repairs at night or on weekends cost extra, sometimes double the normal rate
- Travel fees for remote locations – If your business is far from the service provider, you may be charged extra for travel.
- Specialized part replacements – Some HVAC systems need unique parts that cost more and take longer to arrive.
- Permit or inspection fees – Major repairs or upgrades may require state or local permits, adding to the total cost.
Always ask for a detailed quote before agreeing to service. Also, check with your provider to see if there are any state permit fees you should expect.
Take Control of Your HVAC Costs
Keeping your HVAC system in good shape helps your business save money and avoid unexpected expenses. Regular check-ups, emergency repair costs, labor wages, and state rules all affect your HVAC budget. Planning ahead can help you stay in control.
Many businesses struggle with sudden failures, high energy bills, and regulation issues. Without a maintenance plan, these problems can become very expensive. But with the right approach, you can keep costs low and your system running smoothly.
Now that you know how much HVAC maintenance costs and why it’s important, take a look at your current plan. Are you keeping up with preventive maintenance? Do you have a trusted HVAC service provider?
If not, consider reaching out to a professional for an affordable maintenance plan.
At Harold Brothers, we help businesses in New Hampshire keep their HVAC systems running smoothly without overspending. If you’re ready to cut costs and avoid HVAC headaches, contact us today for a consultation.
a company gives you a price estimate, extra charges can sometimes surprise business owners. These hidden fees can add up fast, making repairs more expensive than expected.
Watch out for:After-hours or weekend fees – Emergency repairs at night or on weekends cost extra, sometimes double the normal rate.
Travel fees for remote locations – If your business is far from the service provider, you may be charged extra for travel.
Specialized part replacements – Some HVAC systems need unique parts that cost more and take longer to arrive.
Permit or inspection fees – Major repairs or upgrades may require state or local permits, adding to the total cost.
Always ask for a detailed quote before agreeing to service. Also, check with your provider to see if there are any state permit fees you should expect.
Take Control of Your HVAC Costs
Keeping your HVAC system in good shape helps your business save money and avoid unexpected expenses. Regular check-ups, emergency repair costs, labor wages, and state rules all affect your HVAC budget. Planning ahead can help you stay in control.
Many businesses struggle with sudden failures, high energy bills, and regulation issues. Without a maintenance plan, these problems can become very expensive. But with the right approach, you can keep costs low and your system running smoothly.
Now that you know how much HVAC maintenance costs and why it’s important, take a look at your current plan. Are you keeping up with preventive maintenance? Do you have a trusted HVAC service provider?
If not, consider reaching out to a professional for an affordable maintenance plan.
At Harold Brothers, we help businesses in New Hampshire keep their HVAC systems running smoothly without overspending. If you’re ready to cut costs and avoid HVAC headaches, contact us today for a consultation.
With over 39 years of experience in the HVAC industry, Lisa Flynn brings a wealth of knowledge, reliability, and proven leadership to every project. She has a demonstrated track record of managing and mentoring HVAC service technicians while collaborating closely with project managers to ensure the successful execution of construction projects. Lisa's expertise spans a broad range of critical functions, including dispatching service calls, budget preparation and management, billing and collections, and project quoting. She has cultivated strong client and customer relationships through her attention to detail and commitment to delivering exceptional results. From marketing and advertising initiatives to equipment procurement, tracking, and project close-outs, Lisa consistently drives efficiency and excellence at every stage. Her hands-on approach and dedication to exceeding expectations make her a trusted partner for clients and colleagues alike.
Topics: