The True Cost of Preventative Maintenance for VRF Systems
February 4th, 2025
4 min read
By Lisa Flynn
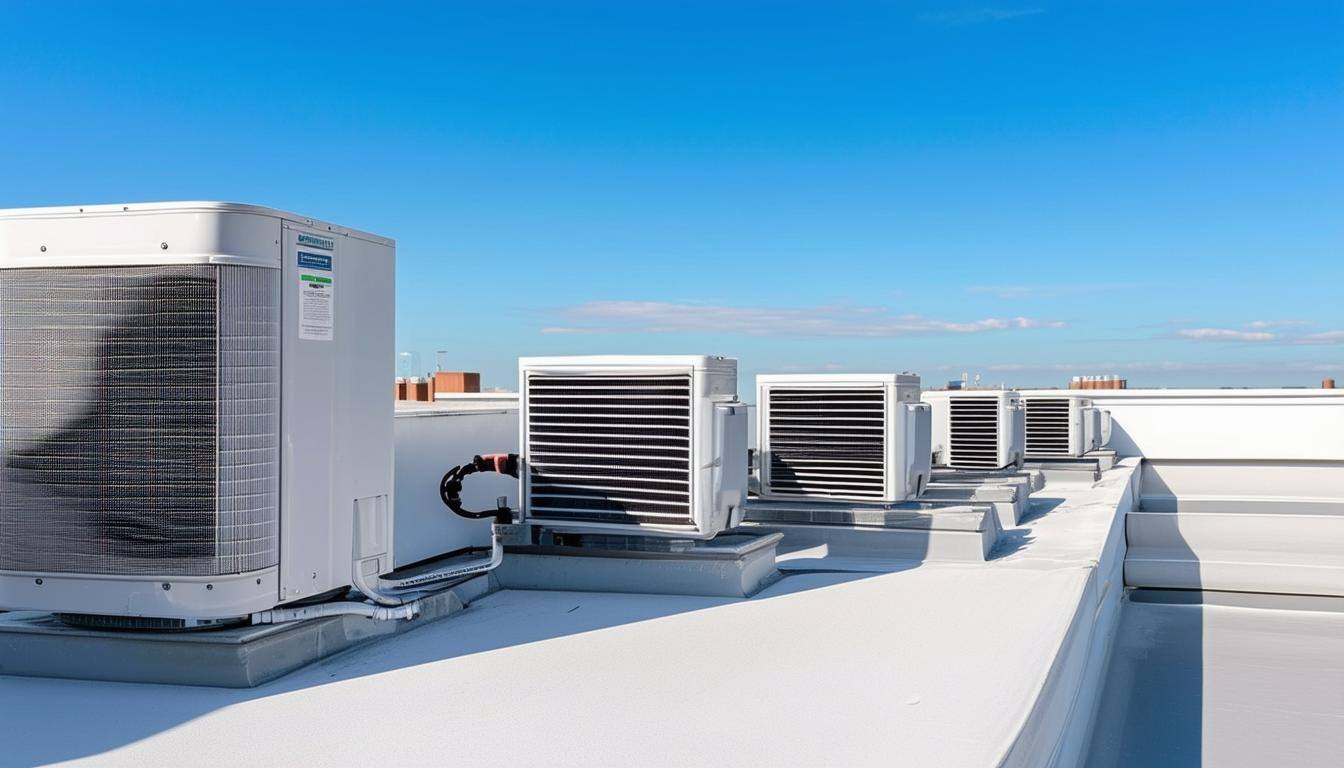
If your VRF system fails, you could be looking at unexpected repair costs, skyrocketing energy bills, or even disruptions to your business operations. Unfortunately, many system owners don’t consider a preventative maintenance (PM) plan—until they’re dealing with a costly emergency.
At Harold Brothers Mechanical, we’ve seen businesses spend thousands on repairs that could have been prevented with regular maintenance. So, what does a preventative maintenance contract actually cost? And more importantly, how does it save you money in the long run?
In this article, we will explore the real costs associated with preventative maintenance for VRF systems, examine the factors that influence pricing, discuss how regular maintenance can prevent costly repairs, and highlight what to look for in a service contract.
By the end, you’ll know whether a preventative maintenance plan is the right investment for your system.
How Much Does VRF Preventative Maintenance Cost?
The cost of a VRF maintenance plan depends on the size and complexity of your system.
Below is a general breakdown:
SYSTEM SIZE | TYPICAL ANNUAL COST |
Small (1-3 Indoor Units) |
$650 – $1,250 |
Medium (4-10 Indoor Units) | $2,500 – $5,000 |
Large (10+ Indoor Units & Complex Configurations) | $5,000 – $40,000+ |
Why the Big Price Range? VRF systems vary greatly in complexity. The more units you have, the more inspections, cleaning, and refrigerant checks are needed to maintain efficiency.
What Determines the Cost of VRF Preventative Maintenance?
Several factors influence where your system falls within the pricing range:
1. System Size & Configuration
More indoor units = more components to inspect and clean.
Larger or multi-zone systems require more refrigerant checks and airflow balancing.
2. Frequency of Service
Semi-annual (twice a year) is the most common schedule.
Quarterly or monthly maintenance contracts cost more but reduce the risk of unexpected failures.
3. Condition of Your System
Well-maintained systems cost less to service.
Neglected systems may require coil cleaning, refrigerant recharges, or part replacements, increasing costs.
4. Included Services
Basic contracts cover filter changes and inspections.
Comprehensive contracts include deep cleaning, refrigerant management, and advanced diagnostics.
Pro Tip: When comparing providers, ask for a detailed breakdown of what’s included. A lower price may mean fewer services.
How Preventative Maintenance Saves You Money
1. Prevents Expensive Breakdowns
Would you rather pay $1,000 per year for maintenance or $10,000+ for a compressor failure? Catching minor refrigerant leaks or airflow issues early prevents major failures. Regular inspections keep electrical components and sensors functioning properly.
2. Improves Energy Efficiency
Dirty coils, clogged filters, and refrigerant imbalances reduce efficiency. Well-maintained systems use less energy, lowering utility costs.
3. Extends System Lifespan
VRF systems are a major investment. Preventative maintenance helps them last 15-20 years instead of failing prematurely.
4. Protects Your Warranty
Most VRF manufacturers require regular maintenance to keep the warranty valid. Skipping maintenance could mean paying out-of-pocket for repairs that should be covered.
What Happens If You Skip Preventative Maintenance?
Ignoring maintenance doesn’t just increase costs—it can cause system failures that disrupt operations. Here’s what you risk:
- Higher Energy Bills – Dirt buildup and refrigerant issues force your system to work harder.
- Unexpected Downtime – A failed compressor or refrigerant leak could shut down your heating/cooling.
- Shorter Equipment Life – A neglected system wears out 30-50% faster than a maintained one.
- Expensive Repairs – A simple filter replacement costs $50, but a failed compressor could cost $10,000+ to replace.
- Voided Warranty – Many manufacturers require proof of maintenance for warranty claims.
The Bottom Line: A small investment in preventative maintenance saves you from massive repair bills and downtime later.
What to Look for in a VRF Maintenance Contract
If you’re considering a service plan, make sure it includes:
- Filter Replacements & Cleaning – Prevents dust buildup that reduces efficiency.
- Coil & Drain Pan Cleaning – Avoids mold, odors, and water damage.
- Refrigerant Checks – Ensures proper levels to prevent compressor damage.
- Electrical Inspections – Identifies failing components before they cause system failure.
- Airflow & Sensor Calibration – Maintains consistent temperature control across zones.
Not all providers offer the same level of service, so always compare maintenance plans carefully.
Final Thoughts: Is a VRF Preventative Maintenance Plan Worth It?
Preventative maintenance is not merely an expense; it is an investment that safeguards your VRF system, minimizes energy waste, and averts costly repairs.
To recap, annual VRF maintenance costs can range from $650 to over $40,000, depending on the system size and contract specifics. Neglecting maintenance can result in expensive breakdowns, increased energy bills, and even voided warranties.
A well-maintained VRF system not only lasts longer but also operates more efficiently and is less costly to run.
Are you ready to protect your VRF system? At Harold Brothers Mechanical, we have helped businesses save thousands by preventing costly failures. Contact us today to get a Quote!
Ignoring maintenance doesn’t just increase costs—it can cause system failures that disrupt operations. Here’s what you risk:
Higher Energy Bills – Dirt buildup and refrigerant issues force your system to work harder.
❌ Unexpected Downtime – A failed compressor or refrigerant leak could shut down your heating/cooling.
❌ Shorter Equipment Life – A neglected system wears out 30-50% faster than a maintained one.
❌ Expensive Repairs – A simple filter replacement costs $50, but a failed compressor could cost $10,000+ to replace.
❌ Voided Warranty – Many manufacturers require proof of maintenance for warranty claims.
💡 The Bottom Line: A small investment in preventative maintenance saves you from massive repair bills and downtime later.
What to Look for in a VRF Maintenance Contract
If you’re considering a service plan, make sure it includes:
✅ Filter Replacements & Cleaning – Prevents dust buildup that reduces efficiency.
✅ Coil & Drain Pan Cleaning – Avoids mold, odors, and water damage.
✅ Refrigerant Checks – Ensures proper levels to prevent compressor damage.
✅ Electrical Inspections – Identifies failing components before they cause system failure.
✅ Airflow & Sensor Calibration – Maintains consistent temperature control across zones.
Not all providers offer the same level of service, so always compare maintenance plans carefully.
Final Thoughts: Is a VRF Preventative Maintenance Plan Worth It?
Preventative maintenance isn’t just a cost—it’s an investment that protects your VRF system, reduces energy waste, and prevents expensive repairs.
🔹 Recap: What You’ve Learned Today
✔ Annual VRF maintenance costs range from $650 – $40,000+, depending on system size and contract details.
✔ Skipping maintenance can lead to costly breakdowns, higher energy bills, and even voided warranties.
✔ A well-maintained VRF system lasts longer, runs more efficiently, and costs less to operate.
📞 Ready to Protect Your VRF System?
At Harold Brothers Mechanical, we’ve helped businesses save thousands by preventing costly failures.
📩 Get a free quote today! Call 781-871-2111 or visit www.haroldbros.com to learn more.
With over 39 years of experience in the HVAC industry, Lisa Flynn brings a wealth of knowledge, reliability, and proven leadership to every project. She has a demonstrated track record of managing and mentoring HVAC service technicians while collaborating closely with project managers to ensure the successful execution of construction projects. Lisa's expertise spans a broad range of critical functions, including dispatching service calls, budget preparation and management, billing and collections, and project quoting. She has cultivated strong client and customer relationships through her attention to detail and commitment to delivering exceptional results. From marketing and advertising initiatives to equipment procurement, tracking, and project close-outs, Lisa consistently drives efficiency and excellence at every stage. Her hands-on approach and dedication to exceeding expectations make her a trusted partner for clients and colleagues alike.
Topics: