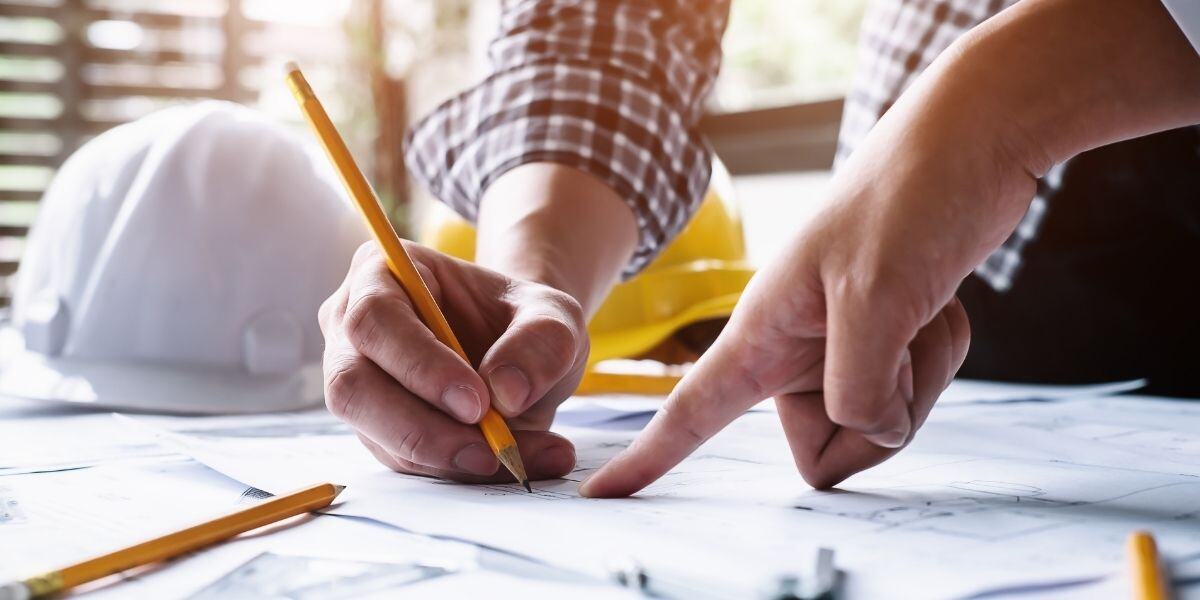
If you’re planning an HVAC installation, you might expect a simple cost calculation based on square footage. But have you ever received two drastically different quotes for similar-sized buildings? It’s frustrating when a rough estimate doesn’t match reality, leaving you wondering what actually determines the price.
At Harold Brothers, we’ve worked with countless commercial HVAC projects in Massachusetts, and we’ve seen firsthand how misleading square footage-based pricing can be. The truth is, that factors like building layout, system type, energy efficiency, and labor all play a major role in determining the final cost.
In this article, we’ll break down the real variables that impact HVAC installation costs—so you can budget accurately and avoid costly surprises.
Average HVAC Cost Per Square Foot in Massachusetts
For commercial buildings in Massachusetts, HVAC installation costs generally fall between $15 to $90 per square foot, depending on the type of system and the complexity of the project. We know this is a huge range, but let’s start here for simplicity's sake. Some general estimates include:
- Office buildings: $15 - $60 per square foot
- The price could be driven up depending on the layout of the space, and the size of the server room or rooms.
- Retail spaces: $17 - $25 per square foot
- The use of the space could drive the cost up, a TV or Tech store would require more cooling and ventilation that a clothing store
- Warehouses & Industrial Facilities: $10 - $90 per square foot
- Restaurants & Hospitality: $25 - $40 per square foot
- Restaurants and Hospitality applications are higher due to their ventilation needs.
For example, if you’re installing HVAC in a 5,000-square-foot office space, the cost could range from $75,000 to $300,000. However, these numbers can quickly change based on additional variables.
Imagine trying to price a car solely based on its size—a small sedan should cost less than an SUV, right? But what about features, fuel efficiency, brand, technology, and customizations?
A basic compact car could be cheaper than a luxury sedan that’s the same size. The same logic applies to HVAC. Two 5,000-square-foot buildings could have drastically different HVAC costs based on their design, insulation, and system needs.
Key Factors That Impact HVAC Costs Other than Square Footage-1.jpg?width=1200&height=600&name=Untitled%20design%20(2)-1.jpg)
1. Building Design & Layout
The shape and design of a building greatly influence HVAC installation costs. A simple, open-floor warehouse will require significantly less ductwork than a multi-story office building with numerous walls and small rooms. Factors that affect HVAC complexity include:
- Ceiling height: Taller ceilings require more powerful heating and cooling units.
- Number of floors: Multi-story buildings require complex air distribution systems.
- Building shape: Irregular layouts need customized ductwork, increasing costs.
2. System Type & Configuration
Different HVAC systems come with different price points. The two most common configurations are:
- Two-pipe system: Costs around $15 - $18 per square foot. Provides either heating or cooling but not both simultaneously.
- Four-pipe system: Costs $18 - $21 per square foot. Allows simultaneous heating and cooling in different areas of a building.
More advanced systems like VRF (Variable Refrigerant Flow), which allow for highly efficient temperature control, can increase costs but provide long-term savings on energy bills.
3. Energy Efficiency & Equipment Quality
Opting for high-efficiency HVAC systems might mean a higher upfront cost but can significantly reduce long-term operating expenses. For example:
- A standard-efficiency rooftop unit may cost $5,000 - $50,000.
- A high-efficiency unit with better SEER (Seasonal Energy Efficiency Ratio) ratings could cost $50,000 - $600,000 but save 20-30% on energy bills annually.
In Massachusetts, where winters are harsh, choosing an energy-efficient system is particularly important to reduce heating costs.
4. Labor Costs & Installation Complexity
Labor is one of the biggest cost variables in HVAC installation. In Massachusetts, HVAC labor rates can range from $75 to $150 per hour, depending on the complexity of the job. Additional labor costs may arise from:
- Retrofitting older buildings which could require asbestos removal or ductwork modifications.
- Installing rooftop HVAC units would require cranes or specialized equipment.
- Custom ductwork fabrication would be necessary for irregularly shaped buildings.
5. Local Regulations & Permitting Costs
Massachusetts has strict building codes and environmental regulations, which can impact installation costs. Businesses must account for:
- Building permits, which can range from $20 to $1,000 depending on the project scope.
- Energy efficiency requirements, such as compliance with the Massachusetts Stretch Energy Code, which may require higher efficiency equipment.
- Refrigerant regulations, as older refrigerants like R-22 and R410A are being phased out and replaced with more eco-friendly options, like A2L Refrigerant.
6. Building Usage & Occupancy
The function of the building plays a huge role in determining HVAC requirements. For example:
- A data center requires powerful cooling systems to handle heat from servers.
- A restaurant needs extensive ventilation for kitchen exhaust systems.
- A warehouse may only need heating in certain sections, reducing overall costs.
Think of HVAC as heating a home versus a tent. If you only consider square footage, you might assume heating a 1,000-square-foot tent and a 1,000-square-foot house should cost the same. But the house is insulated, while the tent leaks heat, requiring far more energy to maintain a comfortable temperature. Similarly, an HVAC system’s cost is highly dependent on insulation, ventilation, and how efficiently air is distributed—not just the building’s size.
Why You Can’t Just Use Square Footage for Pricing
At the end of the day, determining HVAC costs based solely on square footage is a misleading approach. The reality is that multiple factors—including building layout, system type, energy efficiency, labor, and local regulations—significantly impact the final price.
You likely started this journey frustrated by inconsistent HVAC quotes, wondering why similar-sized buildings have such different costs. Now, you have a clearer understanding of the key cost drivers and how to approach your HVAC budget with a more informed perspective.
Your next step? Work with a qualified HVAC contractor who can assess your specific building needs and provide a tailored cost estimate. This ensures you’re making a smart investment in a system that fits your budget while optimizing long-term efficiency. Contact Harold Brothers today for a quote.
Dennis Allen is the Chief Operating Officer and the Director of HVAC for Harold Brothers Mechanical. His current role includes overseeing daily operations in all aspects of the HVAC department from Estimating, Project Management, Equipment and Subcontractor procurement through completion of all HVAC projects. Dennis currently lives in Marshfield, Ma with his Wife of 15 years and their 2 children. Dennis is very involved in town youth sports and volunteers with Marshfield Youth Soccer and Hockey. You will see him at hockey rinks and soccer fields throughout New England on most weekends, when Dennis is not at the rink or fields, he enjoys spending time with family and friends and is frequently spotted fishing in Duxbury Harbor. Dennis takes pride in his upbringing in the mechanical industry, he started as an apprentice in 2001 and has worked his way up through hard work and dedication in his field. He has worked on multiple large-scale projects throughout his career and credits his development to the tradesman who took him under their wing and provided the knowledge needed to succeed. In his current role he works closely with property owners and engineers to assure each and every project is designed to meet each client’s needs. He is very passionate in the success of the younger generation getting into the field and has donated his time to teach and educate field personnel on how to interpret design documents, installation practices and understanding of current codes. He believes all people regardless of background should be given the opportunity to enter the Pipefitting/Refrigeration industry and be set up for success. He recognizes that his industry is facing a major skilled trade shortage and is firm in his belief that training and education should be made available to all people looking to enter the trade. In 2016 he had the foresight to see our industry was evolving to more energy efficient systems and took a trip to Japan to educate himself on the Variable Refrigerant Flow systems which we currently see being implemented in designs throughout the commonwealth. The people of Japan have been utilizing this technology since the 1970’s and provided invaluable insight into how these systems get manufactured, installed and operate. In 2024 Dennis was appointed a member of the Massachusetts Board of Pipefitters, Refrigeration Technicians, and Sprinkler Fitters.