Preventing Commercial HVAC Problems Before They Begin
February 11th, 2025
4 min read
By Dennis Allen
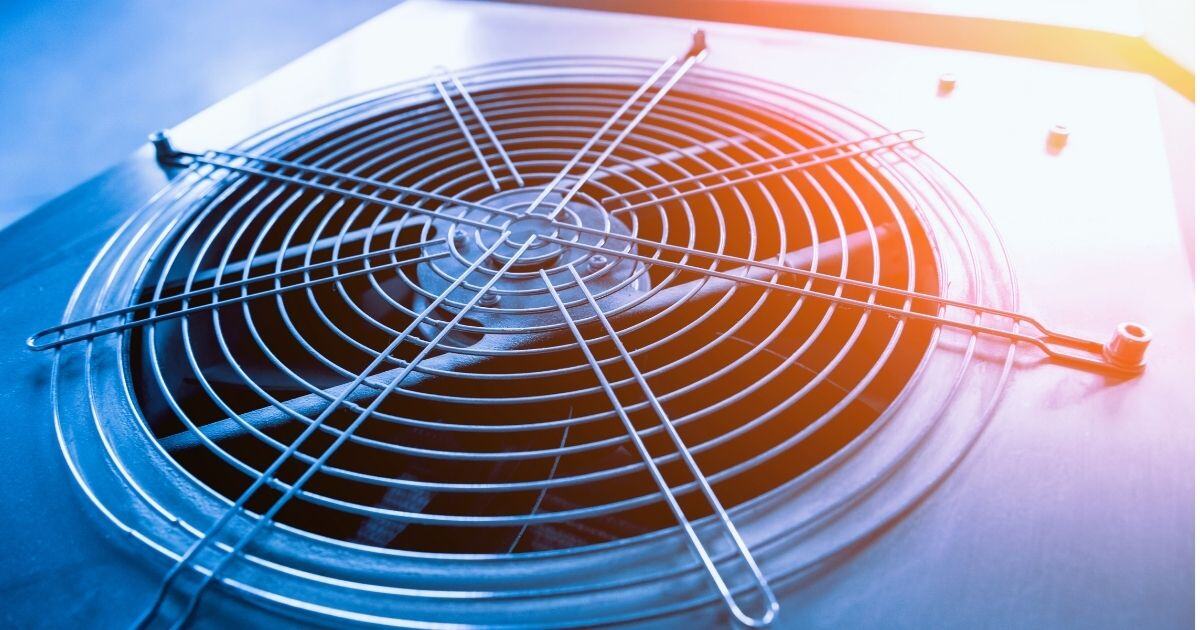
If your HVAC system isn’t properly maintained, you’re likely experiencing rising energy bills, unexpected breakdowns, and complaints from tenants or employees about discomfort with temperature. These issues can disrupt functions and raise financial and safety concerns.
Harold Brothers has spent 16 years helping commercial building owners avoid these issues. With our expertise in HVAC maintenance, we’ve seen how disregarding routine care can cause systems to fail much earlier.
In this article, we’ll show you how skipping HVAC preventative maintenance can affect your system. You’ll learn about the most common risks, from energy inefficiency to safety hazards, and how proactive care can protect your HVAC system, improve comfort, and save you money in the long run.
The Cost of HVAC Inefficiency on Your Commercial Building
An HVAC system is designed to cool and heat your building properly throughout the seasons. However, without regular maintenance, it starts to lose efficiency. Dirty coils, clogged filters, and general wear and tear force the system to work harder to produce the same level of heating or cooling. This can translate directly into higher energy bills.
For example, a neglected system can lose between 5% and 15% of its ability to heat or cool annually. Over time, this can mean thousands of dollars wasted on energy costs. Many commercial building owners don’t realize that a poorly maintained HVAC system impacts their budget and their environmental footprint. Higher energy consumption contributes to unnecessary carbon emissions, making your building less sustainable.
Preventative maintenance, such as cleaning coils and replacing filters, ensures your system operates at its peak. It’s a small investment that pays off in lower energy costs and a greener footprint for your building.
Shorter System Lifespan
An HVAC system is a big investment for any building. If you take good care of it, it can last 15 to 20 years. But if you don’t keep up with maintenance, it won’t last nearly as long. Small problems, like a loose belt or a clogged filter, can make the system work harder, causing it to wear out faster.
For example, the compressor is one of the most expensive parts of an HVAC system. Replacing it can cost between $8,000 and $10,000. If it has to work too hard because of neglect, it can break sooner, leading to costly repairs or replacements. Skipping regular maintenance could mean paying to replace the whole system much earlier than expected.
Regular check-ups help catch small problems before they get worse. Fixing these issues early can save money and keep your system running longer without unexpected breakdowns.
Compromised Indoor Air Quality
Skipping HVAC maintenance can affect the air quality inside your building. The HVAC system moves air through the building, but if it’s not properly cared for, the air can carry dust, allergens, and even mold.
Dirty filters and ducts allow these pollutants to spread, leading to poor air quality. This can cause health problems like breathing issues, allergies, and more sickness. This is especially dangerous for places like schools, hospitals, or senior living homes where people may already be at risk.
Bad air quality can also lead to complaints. Buildings with poor airflow may lose tenants, which can hurt your reputation. Regular maintenance keeps filters and ducts clean and improves airflow, making the building healthier and more comfortable for everyone.
The High Cost of Emergency Repairs
Some building owners think they save money by skipping HVAC maintenance, but it’s actually the opposite. Emergency HVAC repairs cost much more than regular maintenance. When a system breaks down unexpectedly, repairs can be very expensive. It can also cause problems for tenants or businesses in the building.
For example, if a compressor breaks because of neglect, replacing it can cost over $8,000 for the part alone. Adding the cost of installation could raise the total to $15,000. On the other hand, regular maintenance plans cost much less each year. They also help technicians find and fix small problems before they become big ones.
Think of HVAC maintenance like getting an oil change for your car. It’s a small cost that helps avoid bigger, more expensive problems later. Skipping maintenance might seem like a way to save money, but it often ends up costing much more.
Safety Risks
A neglected HVAC system can be dangerous, not just costly. Broken electrical parts can cause fires, and damaged heating systems can lead to gas leaks. One of the most serious dangers is carbon monoxide poisoning, which can happen if a heating system isn’t taken care of properly.
Carbon monoxide is a gas you can’t see or smell, but it can be deadly in large amounts. Regular maintenance makes sure your HVAC system is venting correctly and repairs any leaks before they become dangerous.
Safety checks are an important part of maintenance. Technicians look at electrical connections, gas lines, and other parts to make sure everything is secure. This helps keep people in the building safe and protects you from legal problems if something goes wrong.
Preventative Maintenance: A Smart Investment
Preventative maintenance isn’t just about avoiding problems—it’s about maximizing the value of your HVAC system. A proactive approach guarantees that your system operates efficiently, lasts longer, and keeps your tenants or employees comfortable. It’s a long-term investment for the health of your building and the happiness of the occupants.
By partnering with a professional HVAC service technician, you can create a maintenance plan tailored to your building’s specific needs. Regular inspections, cleaning, and minor repairs can prevent most of the issues we’ve discussed, saving you money and stress in the long run.
Don’t Wait Until It’s Too Late
Neglecting preventative HVAC maintenance can lead to higher costs, lower resident satisfaction, and even serious safety hazards. From wasted energy and poor indoor air quality to emergency repairs and shortened system lifespan, the consequences of skipping maintenance are far-reaching.
The good news is that these problems are preventable. By investing in routine maintenance, you can protect your building’s HVAC system, save money, and provide a safe and comfortable environment for everyone inside.
At Harold Brothers, we’ve helped countless building owners like you develop preventative maintenance plans that reduce costs and extend the life of their HVAC systems. Ready to take the next step? Schedule an inspection with our service team today and discover how preventative maintenance can make all the difference for your building!
Dennis Allen is the Chief Operating Officer and the Director of HVAC for Harold Brothers Mechanical. His current role includes overseeing daily operations in all aspects of the HVAC department from Estimating, Project Management, Equipment and Subcontractor procurement through completion of all HVAC projects. Dennis currently lives in Marshfield, Ma with his Wife of 15 years and their 2 children. Dennis is very involved in town youth sports and volunteers with Marshfield Youth Soccer and Hockey. You will see him at hockey rinks and soccer fields throughout New England on most weekends, when Dennis is not at the rink or fields, he enjoys spending time with family and friends and is frequently spotted fishing in Duxbury Harbor. Dennis takes pride in his upbringing in the mechanical industry, he started as an apprentice in 2001 and has worked his way up through hard work and dedication in his field. He has worked on multiple large-scale projects throughout his career and credits his development to the tradesman who took him under their wing and provided the knowledge needed to succeed. In his current role he works closely with property owners and engineers to assure each and every project is designed to meet each client’s needs. He is very passionate in the success of the younger generation getting into the field and has donated his time to teach and educate field personnel on how to interpret design documents, installation practices and understanding of current codes. He believes all people regardless of background should be given the opportunity to enter the Pipefitting/Refrigeration industry and be set up for success. He recognizes that his industry is facing a major skilled trade shortage and is firm in his belief that training and education should be made available to all people looking to enter the trade. In 2016 he had the foresight to see our industry was evolving to more energy efficient systems and took a trip to Japan to educate himself on the Variable Refrigerant Flow systems which we currently see being implemented in designs throughout the commonwealth. The people of Japan have been utilizing this technology since the 1970’s and provided invaluable insight into how these systems get manufactured, installed and operate. In 2024 Dennis was appointed a member of the Massachusetts Board of Pipefitters, Refrigeration Technicians, and Sprinkler Fitters.
Topics: