What is the Cost of Commercial HVAC Maintenance in Massachusetts?
January 13th, 2025
4 min read
By Dennis Allen
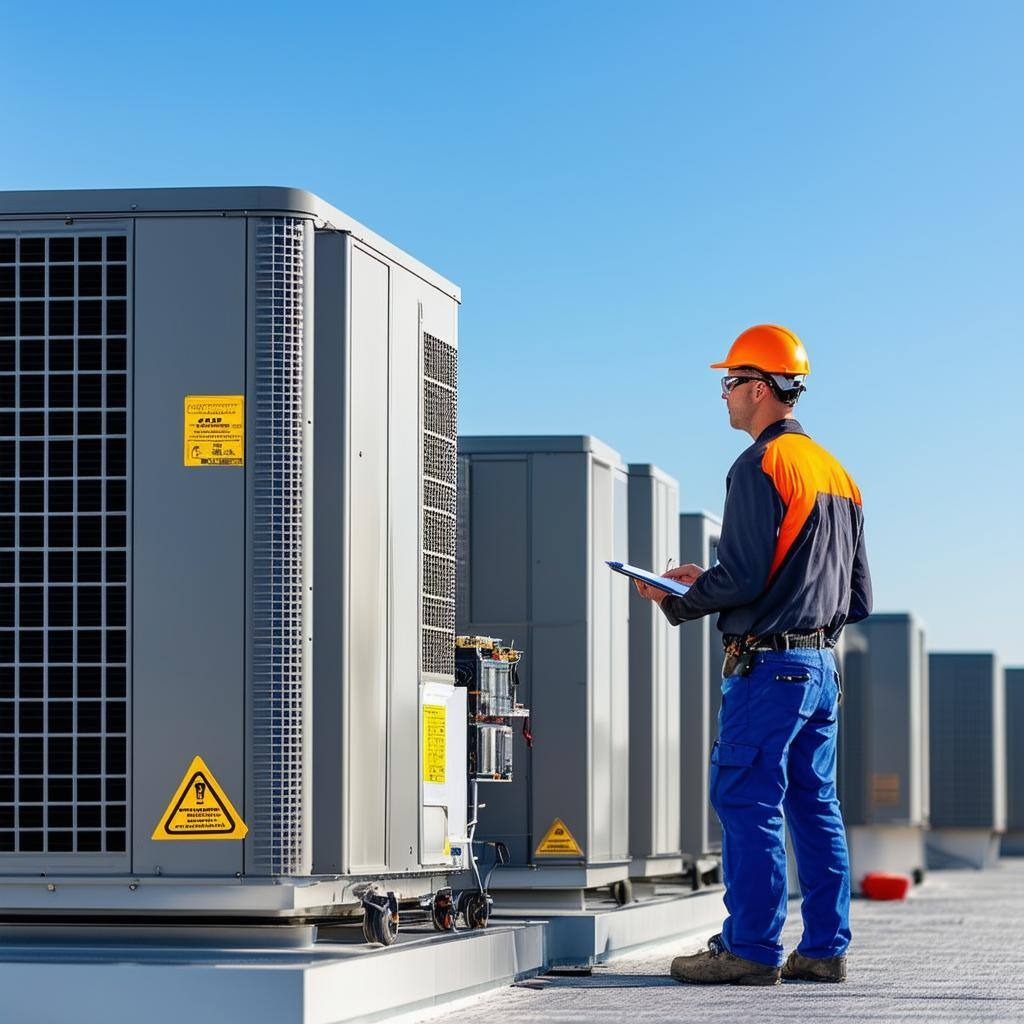
Knowing what to expect when maintaining your commercial HVAC system can be tricky. You might have just installed a new system and want to know the best way forward. Or, you might be in a position where an unexpected issue has popped up and now you have to figure out how to deal with a potentially expensive fix.
We have had customers call after having an HVAC system for a year or two with no problems then all of a sudden the heat just won’t turn on in the middle of January, or on the hottest day of the summer, there’s no cold air.
Harold Brothers has been helping customers with these types of calls and more since 2008, which is why we understand the importance of routine maintenance checks on all your commercial units. That’s why we’re here to help you in understanding your unique HVAC system, and all that might come along in trying to maintain it. This will ultimately help you to budget, and get a longer life out of your HVAC.
In this article, we will help you take charge of your HVAC system expenses and know what is involved with maintaining it, as well as what potential costs might be in your future.
Let’s start with the essentials first.
Essential HVAC Maintenance Tasks
The first thing you can do to set yourself up for success is invest in a Preventative Maintenance Contract (PM). This is a package you can purchase to have a professional come in and regularly perform maintenance on your HVAC system.
Most HVAC companies offer a PM of some sort where they will come in and care for your system and help you to get the longest life out of your system.
A standard Preventative Maintenance Contract will include at least:
Filter ReplacementsChecking Electrical Connections on Each Unit
Checking Condenser Coils
Cleaning as needed
Removing any Debris Around Air Intakes or Condenser Sections
- Filter Replacements
- Checking Electrical Connections on Each Unit
- Checking Condenser Coils
- Cleaning as needed
- Removing any Debris Around Air Intakes or Condenser Sections
If you have onsite maintenance, your team should be checking the system regularly. Filters should be checked once a month and most must be replaced every three months. Filter costs range from $ 5 for standard cardboard filters to $5,000 for ceramic filters.
One of the benefits of a PM is that licensed professionals know exactly what coils, filters, pumps, or temperatures need to be checked. They also know how to clean or regulate any part of your system.
When you invest in a PM you can choose what you want to have included in that plan. Maintenance plans can range from a standard PM where the company will come in and just do filter changes and visual inspections. To a more involved maintenance plan, which would encompass all pieces of equipment, and all degrees of maintenance. From motor replacements to belts and sheaves, refrigeration charges, pressure gages, pumps, and pump seals.
Essential Maintenance Plan Costs
You also need to be aware that different systems have different costs associated with them, for example, if you have a Lochinvar Boiler. This is a reliable boiler but you still need to perform maintenance on it like every other brand.
So, you would need to purchase a maintenance kit annually to make sure that your system stays in peak performance. The cost of a maintenance kit for that particular brand can vary anywhere between $300.00 to $1000.00.
This is an example of the costs you need to plan on to maintain your HVAC system. Another example of an annual cost could be changing any belts on your rooftop units the belts themselves might be relatively inexpensive, but do you have someone on staff who is trained to get up onto your roof and do that kind of work?
Having the potentially hazardous work done by a licensed professional is another one of the benefits of investing in a PM. They can range in price, so you do need to contact a service company and have them come out to look at your specific needs to figure out exactly what plan works best for your situation. The range of a PM can vary between $500.00 for someone with a boiler room and a single boiler unit up to $200,000 for someone with multiple rooftop units or a complicated VRF (variable refrigerant flow) system.
Unexpected HVAC Costs You Should Plan For
Say you have a PM and you are doing everything you can to make sure that your HVAC system is in top-notch condition, can you still expect to have unexpected costs? The answer is YES! Unfortunately, sometimes things happen, and you should plan to have some unexpected costs associated with your HVAC system.
The risk of those unexpected costs is higher if you don’t perform regularly scheduled maintenance on your system, but even with that you might run into some problems. Sometimes parts just fail, blower motors fail, and leaks can happen. When you hire someone to look at your system they can catch the signs that something is about to happen and save you from having a costly repair, but they might recommend replacing some of the parts in your system to keep it from failing.
Also, these are machines, just like your car won’t run forever no matter how many times you bring it in for a tune-up, you eventually will need to trade in that 2005 Honda Civic. And just like cars, some boilers last forever like a Honda, and some just don’t give you 20 years. And if you treat your HVAC unit like I treated my first car you might not even see five years without needing to replace your whole system. While we like to keep a system running for as long as possible, as your equipment ages you do need to consider when to replace it.
For example, if you had a 10-ton condenser that was 15 years old, it would be more cost-effective to replace it if you need a new part than it would be to repair it because you would start to need to constantly repair parts and pieces on it moving forward. It would have its usable life expectancy met at 10 to 15 years.
Now That You Have a Better Understanding of Your System’s Needs, What is Next?
So, now that you know you need to plan to care for your system, and that you will probably need to budget for some unexpected costs, what should your next steps be? Harold Brothers wants to give you the tools to make the best decisions possible for your company. Your next step is to figure out if you need a preventative maintenance contract and then we can talk about your specific needs - “The Importance of purchasing a HVAC maintenance contract”
Dennis Allen is the Chief Operating Officer and the Director of HVAC for Harold Brothers Mechanical. His current role includes overseeing daily operations in all aspects of the HVAC department from Estimating, Project Management, Equipment and Subcontractor procurement through completion of all HVAC projects. Dennis currently lives in Marshfield, Ma with his Wife of 15 years and their 2 children. Dennis is very involved in town youth sports and volunteers with Marshfield Youth Soccer and Hockey. You will see him at hockey rinks and soccer fields throughout New England on most weekends, when Dennis is not at the rink or fields, he enjoys spending time with family and friends and is frequently spotted fishing in Duxbury Harbor. Dennis takes pride in his upbringing in the mechanical industry, he started as an apprentice in 2001 and has worked his way up through hard work and dedication in his field. He has worked on multiple large-scale projects throughout his career and credits his development to the tradesman who took him under their wing and provided the knowledge needed to succeed. In his current role he works closely with property owners and engineers to assure each and every project is designed to meet each client’s needs. He is very passionate in the success of the younger generation getting into the field and has donated his time to teach and educate field personnel on how to interpret design documents, installation practices and understanding of current codes. He believes all people regardless of background should be given the opportunity to enter the Pipefitting/Refrigeration industry and be set up for success. He recognizes that his industry is facing a major skilled trade shortage and is firm in his belief that training and education should be made available to all people looking to enter the trade. In 2016 he had the foresight to see our industry was evolving to more energy efficient systems and took a trip to Japan to educate himself on the Variable Refrigerant Flow systems which we currently see being implemented in designs throughout the commonwealth. The people of Japan have been utilizing this technology since the 1970’s and provided invaluable insight into how these systems get manufactured, installed and operate. In 2024 Dennis was appointed a member of the Massachusetts Board of Pipefitters, Refrigeration Technicians, and Sprinkler Fitters.
Topics: